Before Method CNC was officially formed, Max from 26 South Marine and I worked together on a project that perfectly blended our expertise in 3D scanning, design, and digital fabrication. Our task was to create a custom orthopedic wheelchair back support, providing our client with a lightweight, highly functional solution that improved both her comfort and mobility.
The Challenge: Reducing Weight for Easier Handling
The client’s previous wheelchair back support was an off-the-shelf model that was too heavy, particularly when transferring the backrest into her car. She needed something lighter and more manageable, and Max was quick to bring me into the project, knowing that our digital fabrication approach, including CNC milling, 3D printing, composites design, and composites manufacture, could deliver a solution that was both lightweight and durable.
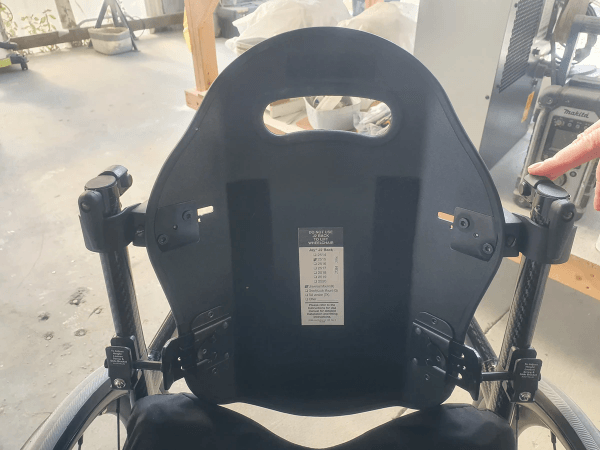
From 3D Scanning to Digital Design
We began by using an EinScan HD2 scanner to capture the detailed contours of the client’s back. This allowed us to create an accurate 3D model, which I reverse-engineered into a NURBS model using Rhino 7. At the time, I printed out four test pieces using a Sidewinder X1 3D printer, as the size of the 3D printer limited us to smaller sections. We have become experts at multi-piece prints, bonding them together and sanding where needed. These four pieces were glued together to test the fit. The feedback from Max was positive—the design met all the critical fitment points. We also conducted a stress simulation to analyze the load distribution through the attachment points, ensuring that the design would be robust enough to handle daily use. During the design phase, we made several smaller pieces redundant by blending the carbon fiber into the complex tube-holding shape, creating a truly custom fit that replaced what had previously been multiple heavy fittings.
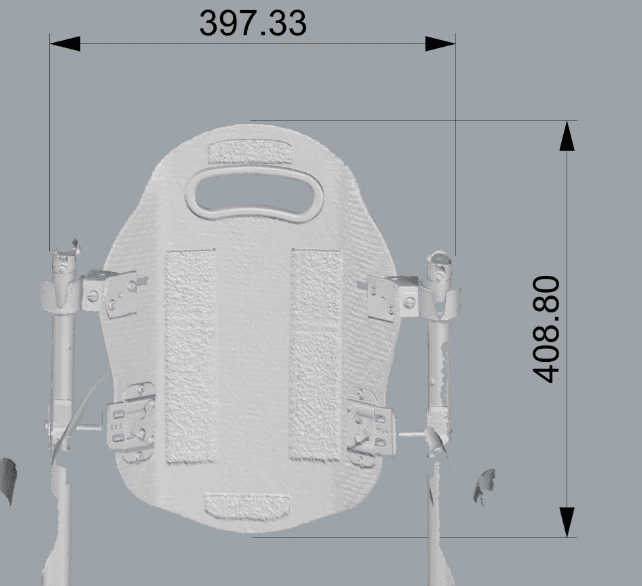
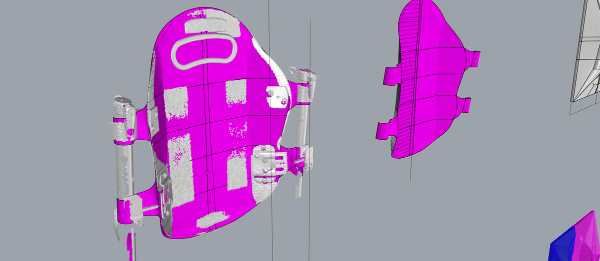
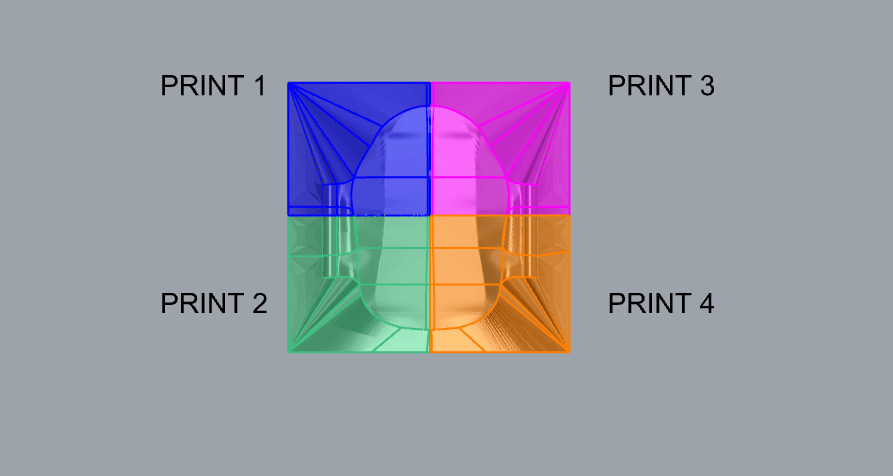
Creating the Final Product: Carbon Fiber and Precision
After the test fit was confirmed, I designed a four-piece mold, which was 3D printed. Max then took over, bonding the mold pieces and using a skim of filler and sanding to remove surface imperfections. He laminated four layers of 400gsm carbon fiber into the mold. Once the material had cured, he trimmed it and drilled the necessary fitment holes.
The final result was a custom, lightweight carbon fiber back support that made the client’s daily routine much easier. She’s still using the backrest today, and we’re proud that our work had such a subtle yet profound impact.
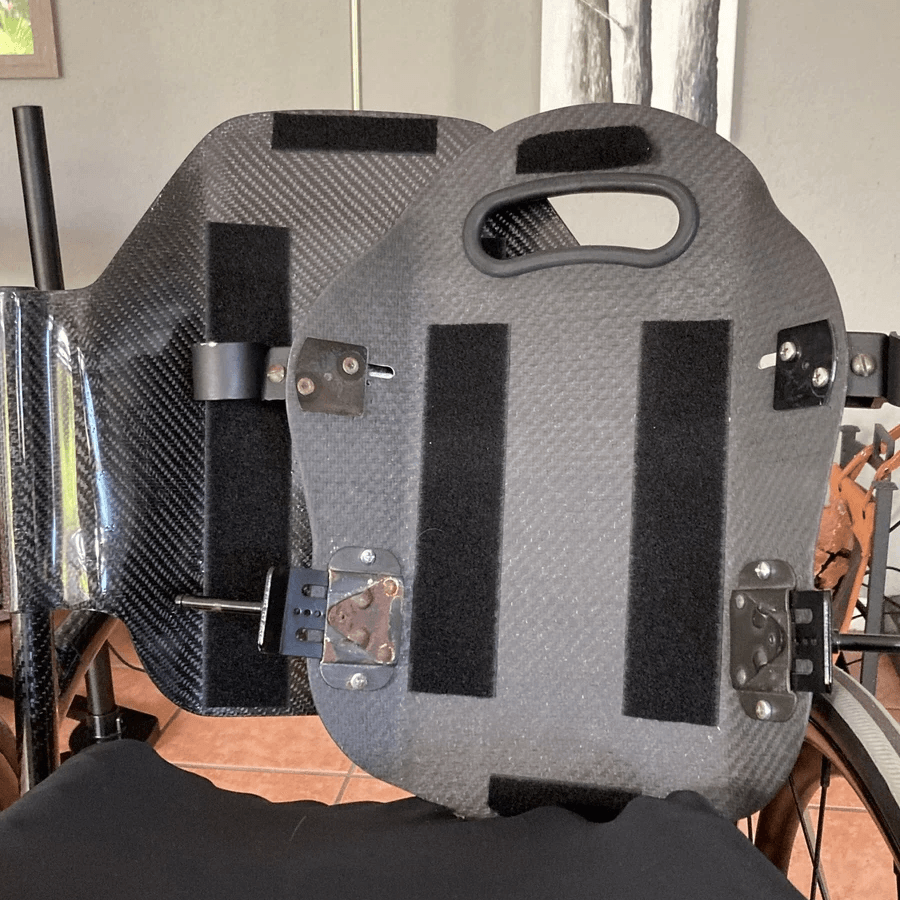
** Above Image - Not the new carbon fibre part in the background that does not have all the metla appendeges that the one in the foreground does. Also based on client feedback we made a few little shape changes to further reduce weight**
Below Image Back View
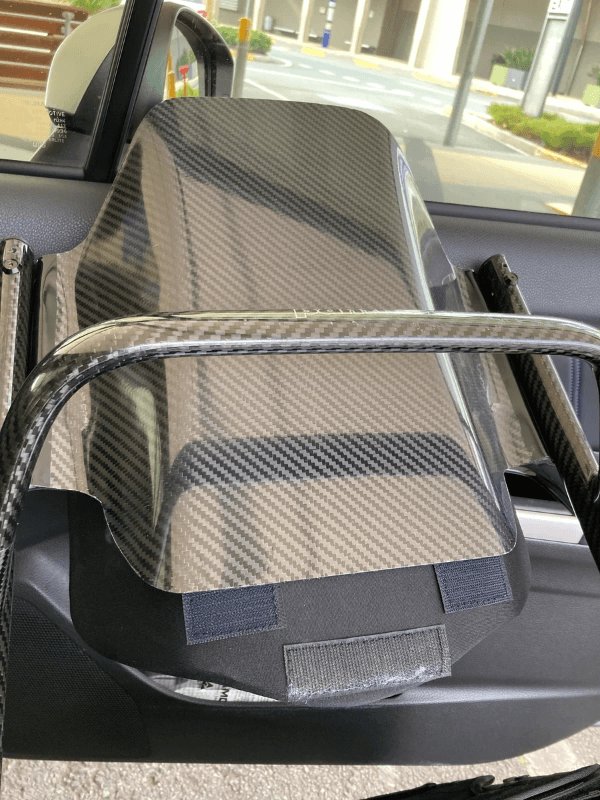
Advancements in Digital Fabrication
If we were to complete this project today, the workflow would look slightly different, thanks to advancements in our available equipment. For this particular job, the mold would now be more suited to CNC machining, allowing us to streamline the process and improve accuracy. Our test fits would still be 3D printed, but we now use a more advanced Bambu 3D printer, and with our CNC machine, we can now go much larger, allowing us to tackle even more ambitious projects.
Precision Design and Fabrication on the Sunshine Coast
This project, though completed before Method CNC was formed, highlights our passion for solving real-world challenges through innovative digital fabrication. Whether it’s using 3D scanning, Rhino modeling, CNC milling, 3D printing, composites design, or composites manufacture, we’re committed to delivering high-quality custom solutions.
If you’re looking for expert design, CNC machining, or 3D printing services on the Sunshine Coast, feel free to reach out to us. We’re here to help bring your ideas to life.